一貫生産体制で純鉄の加工しやすさと低保磁力のバランスを保つ
「純鉄は低炭素鋼より40倍近く透磁率が高く、しかも低保磁力が特徴だ。このため少ない電力で大きな磁場を発生できる。その一方で純鉄は非常に柔らかく、粘土のように粘り気がある。極めて切削しにくい、厄介な材料である」とMPP KOMATSUの代表取締役社長の小松保晴氏(写真)は言う。同社は創業時から製造するボルトで培った鍛造技術を使い、時間をかけて試行錯誤を繰り返し、現在の精密冷間鍛造、精密切削、熱処理による純鉄製リニアソレノイドコアの一貫生産技術に辿り着いた(図3)。「冷間鍛造によって純鉄の大きな組織が細かい緻密な組織に変化する。ちょうど粘土の組織が小砂利を集めたような組織になる。粘土を削るよりも、小さな組織の集合体を削る方がはるかに楽である」と小松氏は説明する。「磁力は組織と組織の間に滞留する。組織が大きい純鉄は磁力が残りにくい。切削の加工しやすさを考えれば完成に近い形まで鍛造で仕上げたいが、その反面保磁力は高まる。加工しやすさと低保磁力はトレードオフの関係にある。そのバランスを保つには一貫生産体制が必要だ。」(小松氏)もちろん、純鉄製リニアソレノイドコアを製造するには高度な切削技術もキーとなる。そのため同社は切削加工技術者のヘッドハンティングも行ったと言う。
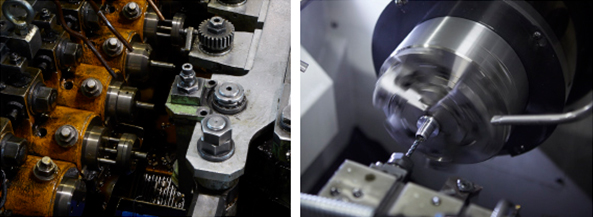
図3●精密冷間鍛造工程(左)と精密切削工程(右)
鍛造と切削両方の製造工程を組むことが出来るため、製品によりお互いの特性を考慮しながら、
最良のバランスになるように微調節することが容易で、製造時間の高速化とコストの最小限化を実現できる。
小松氏は熱処理工程(磁性焼鈍、ガス軟窒化、ろう付け)を自社で行うことの重要性も強調する。例えば、磁性焼鈍は純鉄の保磁力を小さくするため900℃程度で熱処理を行う。しかし、熱処理を行うと金属自体が歪み、リニアソレノイドコアの中空部の径の精度は落ちてしまう。5mmの径に対して許される公差幅はわずか10μmである。「熱処理工程を外注していてはこの精度を満たすことは難しい。ほとんどの外注メーカーは寸法変化までは検査しない。加えてロットによって歪みの仕方も変化する。寸法変化を見越して切削幅を決めなければならない。当社は保磁力を小さくし、かつ、歪みも少なくする熱処理技術のノウハウを取得し、安定した寸法で製造できるようになっている。」(小松氏)。
非自動車分野への普及も目指す
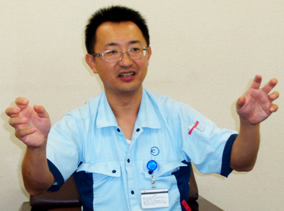
写真●MPP KOMATSUの代表取締役社長の小松保晴氏
MPP KOMATSUは1953年創業の企業である。以前は小松螺子製作という名称だった。螺子はねじと言う意味で、同社は主にオートバイ用ボルトを製造していた。現在、オートバイ用ボルトの生産量が減少して四輪自動車部品の生産量が増えたため、2014年、MPP KOMATSUに社名を変更した。MPPとはMetal Parts Productionの略で、そこには金属部品の一貫生産工場という意味が込められている。
四輪自動車部品進出へのキッカケは2000年ころである。欧米でオートバイの売れ行きが落ち込み、減産に追い込まれた。それに追い打ちをかけたのが円高である。完成車メーカーは、一様に海外生産比率を高め、それに伴いMPP KOMATSUのボルト生産量も落ち込んだ。同時期、現在の新工場へ全面移管したMPP KOMATSUにとって、それは大きな痛手であった。そうした中、前社長の小松常保氏(現代表取締役会長)が四輪自動車部品への進出を決断した。自動車部品を製造する中で2003年ころに精密冷間鍛造技術と精密切削技術が立ち上がった。純鉄製リニアソレノイドコアの量産に結びついたのは2007年である。現在、リニアソレノイドコアの売上は全体の約1/2と、MPP KOMATSUの主力事業に成長した。
小松保晴氏が社長を引き継いだのは2014年である。同氏は、自動車分野における純鉄製リニアソレノイドコアの売上拡大に加え、福祉関連のロボットや航空・宇宙事業など非自動車分野への普及も目指す。「純鉄製リニアソレノイドコアの性能は素晴らしい。しかし製造が難しく世の中にまだそれほど出回ってはいない。当社から世界へ純鉄製リニアソレノイドコアを普及させたい。」と、小松氏は今後の抱負を語る。